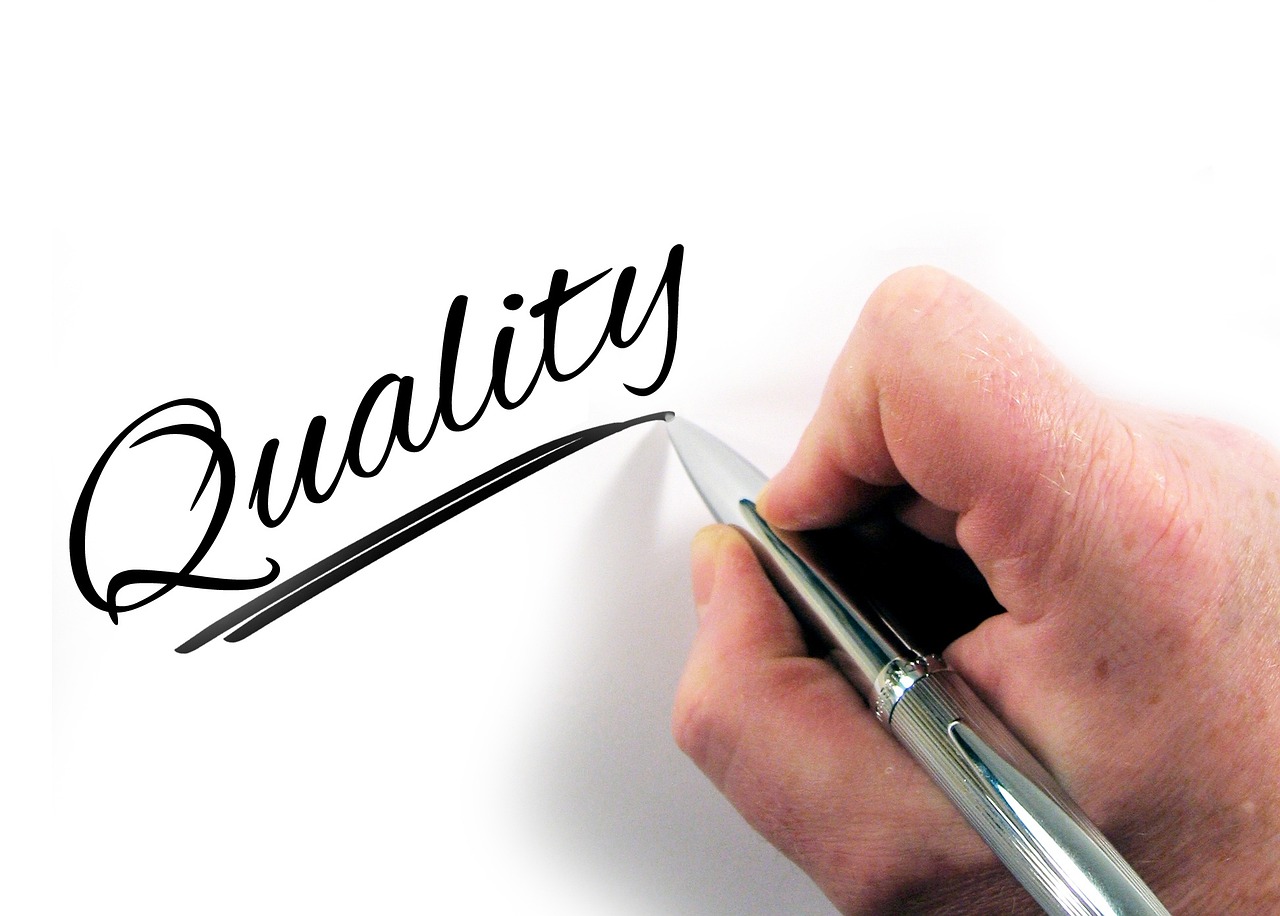
Why Quality Processes Are Essential for Australian Manufacturing—and How to Strengthen Yours
Australian manufacturing community!
We often hear that quality and customer service are what drive customers to choose local manufacturers over competitors or overseas suppliers. It’s a compelling pitch—but too many businesses fall short when it comes to the processes that ensure quality shines through. Let’s unpack what’s missing and how to fix it.
Quality isn’t just about the final product; it’s about the systems behind it. I’ve walked into plenty of operations where high-level quality processes—like non-conformance registers or forms for root cause analysis—aren’t in place. When something goes wrong, are you investigating the root cause? Without these tools, issues can slip through the cracks and keep resurfacing.
Then there’s the matter of quality checkpoints. These systematic reviews ensure everything’s on track at critical stages, but they’re only effective if they’re consistent and your team knows how to handle them. Without proper training or structure, quality becomes a roll of the dice—and that’s a risk we can’t afford.
Here’s what I encourage you to do: take a close look at how you’re tracking quality at a product level. Consider these questions:
How are you documenting issues when they arise?
What’s the real cost of those problems—time, resources, reputation?
Who’s responsible for implementing and following through on corrective actions?
Nailing these elements isn’t just about meeting standards—it’s about exceeding them. Train your team, standardize your checkpoints, and track every issue with precision. That’s how Australian manufacturing builds trust and stays competitive.
What’s your take? I’d love to hear how you’re managing quality in your business—drop a comment or reach out. Let’s keep pushing the industry forward!